R&D Products
Electronic Materials
Harima uses metal-joining technologies to create solder and brazing materials with a host of functions that meet the requirements of the increasingly compact, functional and reliable automotive components and heat exchangers. Our portfolio features highly durable solder materials that can accommodate extreme temperatures, high-density solder pastes for microelectronics, and halogen-free flux materials etc., that meet diverse customer requirements. Our brazing technologies contribute to enhancing heat exchanger efficiency by providing coating materials that facilitate simultaneous welding of tens of thousands of points, residue-free pyrolytic binder resins, and solid, wax-like brazing materials that reduce VOC and energy consumption in manufacturing processes.
Highly Durable Lead-free Solder Pastes
As electronic control of automobiles for increased safety and efficiency has dramatically spread and improved in recent years, customer requirements for solder materials are becoming more diverse and elaborate. To maximize passenger space and comfort, electrical components are placed close to the engine. To accommodate the extreme fluctuations of temperature in this area, Harima has developed highly durable alloys to be employed with our innovative solder pastes.
Closeup of 3216 resistor chip joint
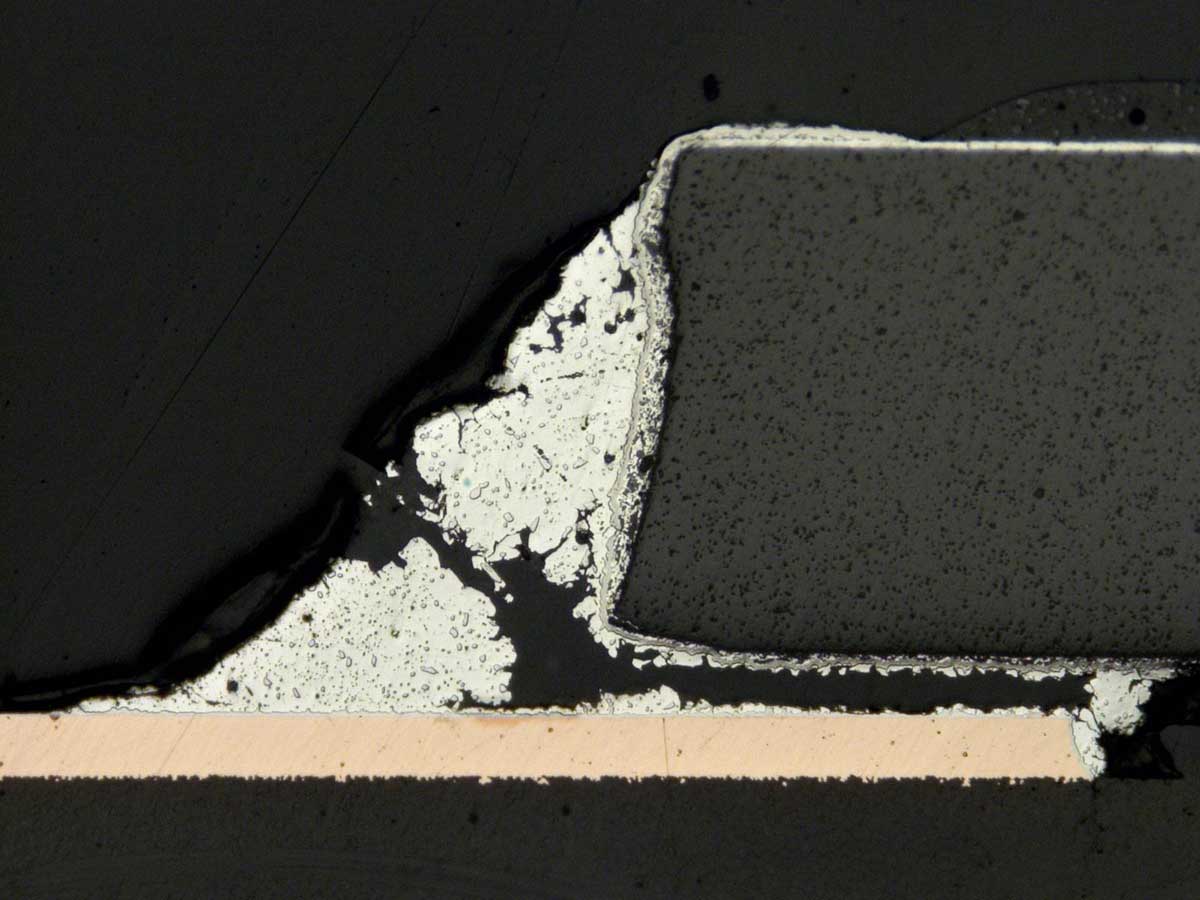
(Sn-3Ag-0.5Cu)
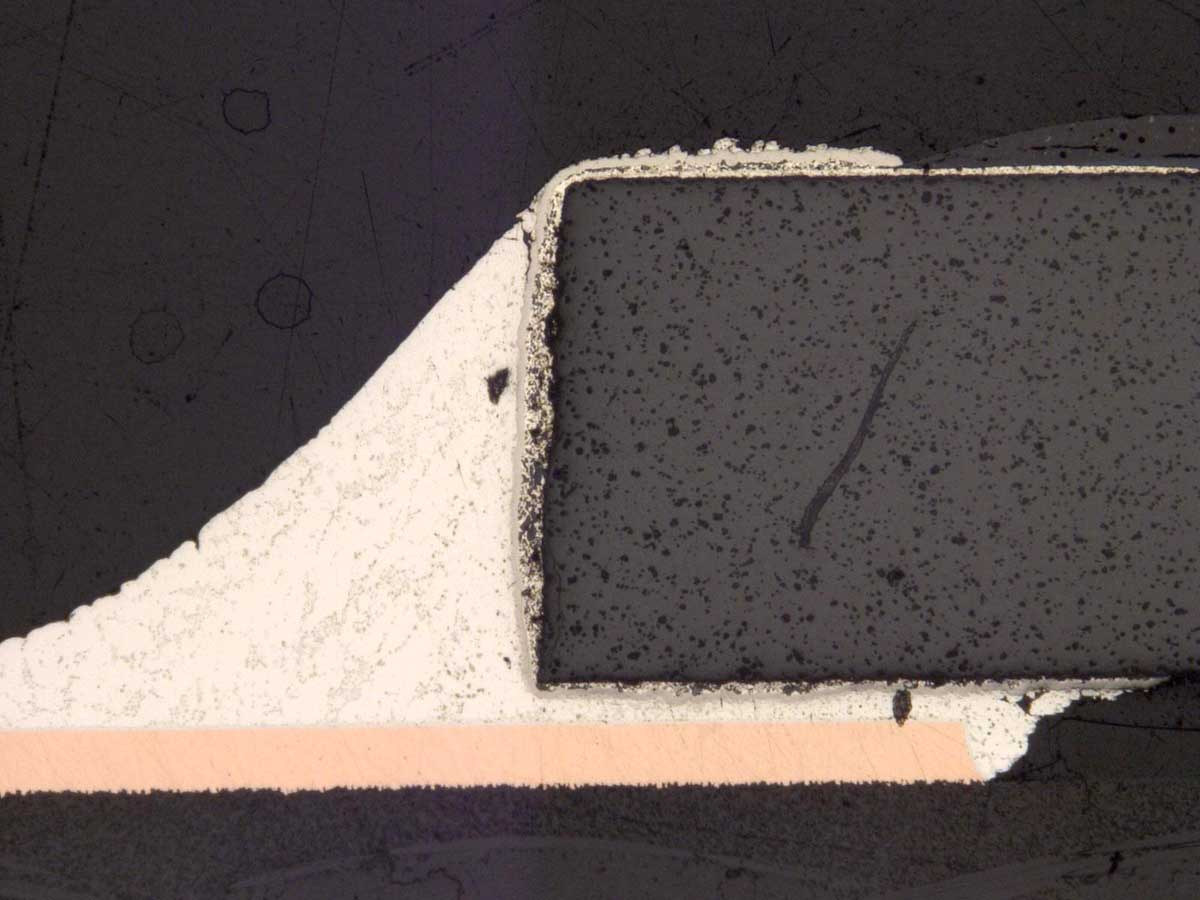
-40℃ ⇔ +125℃ Post-3000cyc
Solid Brazing Materials
Brazing materials used to join metal components in heat exchangers include flux, which removes the oxide film that forms on the surface, and flux paint, a mixture of binder resins and solvents, which enables the adhesion of flux. Conventional application of solid brazing materials requires use of paint rollers or sprays, followed by thermal drying; however, Harima developed wax-like materials that liquify easily and solidify at room temperature without using VOCs, facilitating application and reducing energy consumption during the manufacturing process. These materials, together with the innovative dispensing system that accompanies them, can be successfully used with highly compact and elaborate electronic components.
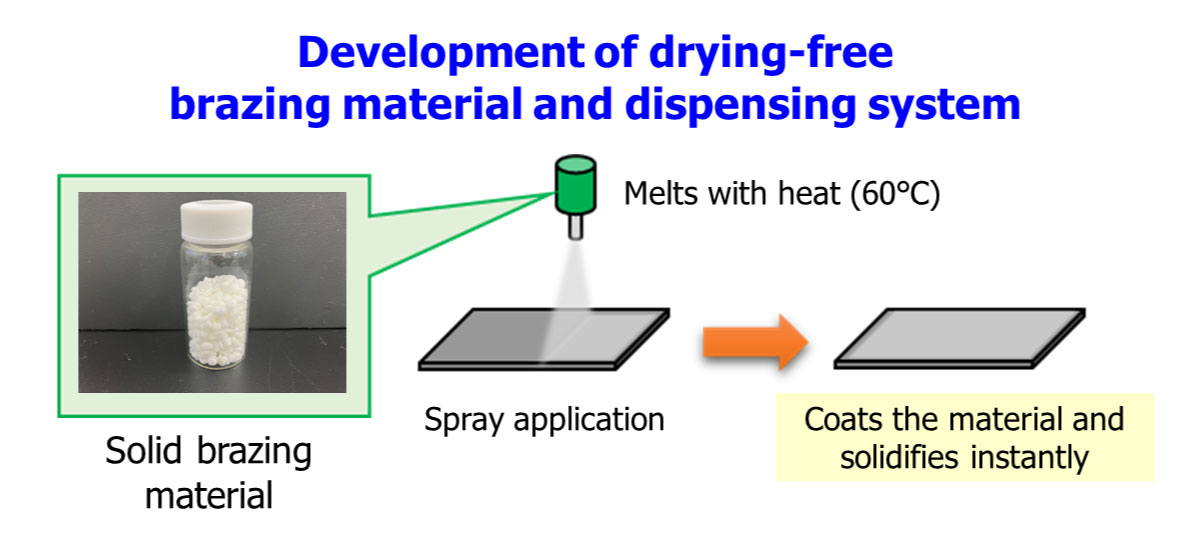